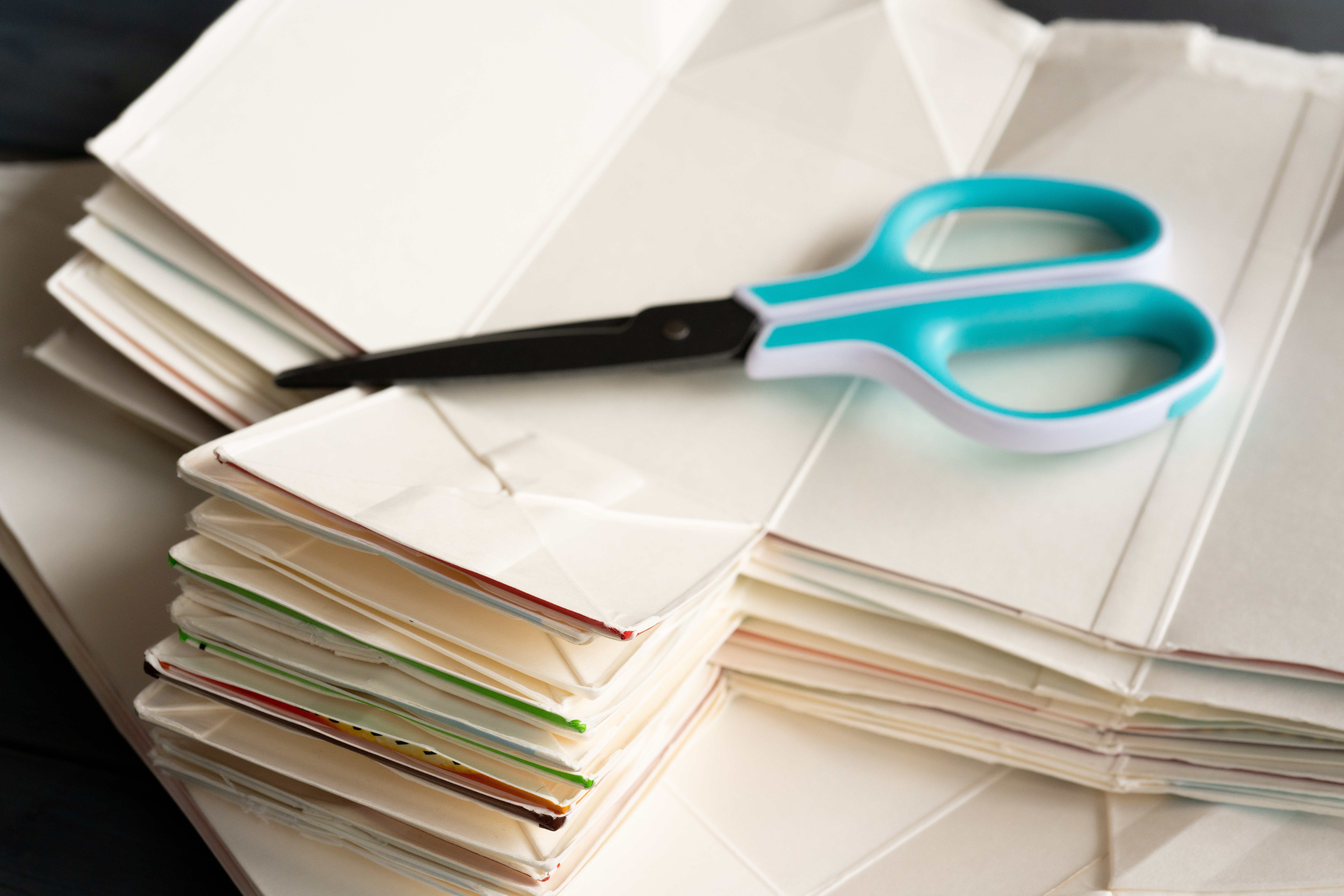
ミルクカートン印刷検査装置:品質向上とコスト削減のメリット
ミルクカートンのパッケージ印刷では、わずかなミスも許されません。品質への厳しい目が向けられる中、目視検査では見落としやコスト増が課題です。
本記事では、大手製造業の技術部門向けに、ミルクカートン印刷検査装置がもたらす品質向上とコスト削減のメリットを解説。検査精度の向上から経営貢献まで、その全貌をお伝えし、貴社の課題解決をサポートします。
1. はじめに:高まる品質要求と製造現場の課題
1.1 消費者からの品質要求の高まりと食品パッケージ印刷の重要性
現代において、消費者の「安心・安全」に対する意識はかつてないほど高まっています。特に、日常的に口にする食品に関わる製品では、わずかな異物混入や表示ミスも許されません。その中でも、子どもから大人まで幅広い世代に親しまれるミルクカートンは、食の安全を象徴するパッケージの一つと言えるでしょう。
パッケージの品質は、製品そのものの信頼性、ひいては企業のブランドイメージに直結します。誤った表示、不鮮明な印刷、色ムラといった軽微な印刷不良であっても、消費者の不信感を招き、最悪の場合、大規模なクレームやリコールへと発展する可能性を秘めているのです。
1.2 ミルクカートン印刷における目視検査の限界と課題
このような状況下で、多くの製造現場では依然として製品の品質検査を目視に頼っているのが現状ではないでしょうか。しかし、ミルクカートンの高速生産ラインにおいて、人の目だけで全ての印刷不良を正確に検出し続けることは極めて困難です。
- 見落としの発生: 人間の集中力には限界があり、長時間の単調な作業は疲労を招き、不良品の見落としに繋がりやすくなります。
- 人件費の増加: 検査員の増員は、人件費の増加を意味し、生産コストを押し上げます。
- 生産性の低下: 目視検査の速度がボトルネックとなり、ライン全体の生産効率を低下させる要因となります。
- 品質のばらつき: 検査員の熟練度や体調によって、検査基準にばらつきが生じることも少なくありません。
1.3 印刷検査装置導入の必要性と、本記事で得られるメリットの提示
これらの課題を解決し、安定した高品質な製品を効率的に供給するためには、人の目に代わる、より高精度で信頼性の高い検査システムが不可欠です。そこで注目されるのが、ミルクカートン印刷検査装置です。
本記事を読み進めることで、貴社は以下のメリットを得ることができます。
- 印刷検査装置の基礎知識と最新技術の理解
- 品質向上とコスト削減という二大メリットの具体的な把握
- 自社に最適な検査装置を選定するためのポイントの習得
これらの情報を通じて、貴社の生産ラインにおける品質管理体制の強化と、経営効率の最大化を実現するための一歩を踏み出しましょう。
2. ミルクカートン印刷検査装置とは?その基礎知識と仕組み
2.1 印刷検査装置の基本的な役割と種類
印刷検査装置とは、製品の印刷面に発生する様々な欠陥を自動で検出し、品質を保証するためのシステムです。主に画像処理技術や光学測定技術を応用しており、人の目では見つけにくい微細な欠陥や、高速で流れるライン上でのリアルタイム検査を可能にします。
主な検査方式としては、以下のようなものがあります。
- パターンマッチング方式: 事前に登録された良品画像と比較し、差異を検出する方法。
- 濃度差検出方式: 印刷の濃淡を数値化し、設定された基準値との差を検出する方法。
- 欠陥分類方式: AIなどを活用し、検出した欠陥を種類別に分類・解析する方法。
これらの技術を組み合わせることで、印刷面全体を網羅的に検査し、不良品を確実に排除します。
2.2 ミルクカートン印刷に特化した検査装置の機能と特徴
一般的な印刷検査装置に加え、ミルクカートンの印刷検査に特化した装置は、その形状や印刷特性に対応するための独自の機能と特徴を備えています。
高速・高精度な欠陥検出(色ムラ、ピンホール、印字不良、異物混入など)
ミルクカートンは、飲料の長期保存性を保つために特殊な多層構造をしており、その表面への印刷は非常に高速で行われます。そのため、検査装置には以下の高精度な検出能力が求められます。
- 色ムラ・色ズレの検出: ブランドイメージを左右する色再現性を厳しくチェックします。
- ピンホール・異物混入の検出: わずかな穴や異物も、内容物の品質に影響を及ぼすため、徹底的に検出します。
- 印字不良・文字欠けの検出: 賞味期限やアレルゲン情報といった重要な表示が正確に印刷されているかを確認します。
- 汚れ・傷・シワの検出: 外観品質を損なう要因を早期に発見します。
多様な印刷方式への対応
ミルクカートンは、オフセット印刷、フレキソ印刷、グラビア印刷など、様々な印刷方式が用いられます。検査装置は、それぞれの印刷方式が持つ特性や発生しやすい欠陥の種類を理解し、それらに柔軟に対応できる汎用性が必要です。例えば、版ズレやインクのにじみなど、印刷方式固有の欠陥も高精度で検出できる機能が求められます。
データ処理・デジタル制御による品質管理
最新の印刷検査装置は、単に欠陥を検出するだけでなく、高度なデータ処理装置とデジタル制御装置を搭載しています。
- リアルタイム解析: 検査結果をリアルタイムで分析し、不良発生の原因を即座に特定できます。
- 傾向分析: 過去の検査データを蓄積・分析することで、印刷工程の傾向を把握し、不良発生を未然に防ぐための改善策を立案できます。
- 統計的品質管理(SQC): 検査データを基に、生産ライン全体の品質を統計的に管理し、プロセスの安定化に貢献します。
- 不良品の自動排出: 検出された不良品を自動的にラインから排出することで、後工程への流出を防ぎます。
これらの機能により、検査装置は単なる「検査ツール」ではなく、「品質管理システム」の中核を担う存在となるのです。
3. 【品質向上】ミルクカートン印刷検査装置導入の具体的なメリット
3.1 検査精度の飛躍的向上と不良品流出ゼロへの貢献
目視検査では困難だった微細な欠陥や、高速生産ラインでの見落としを徹底的に排除できます。装置は人間の疲労とは無縁であり、24時間体制で均一な基準に基づいた検査を継続するため、不良品流出リスクを極限まで低減できます。これにより、顧客からの信頼獲得に大きく貢献し、「不良品ゼロ」という目標に近づくことが可能です。
3.2 品質基準の均一化と標準化
人による検査では、検査員の熟練度や個人の判断基準によって、品質評価にばらつきが生じることが避けられません。印刷検査装置を導入することで、設定された基準に基づき機械が判断するため、品質基準を完全に均一化し、標準化することができます。これは、複数の工場やラインを持つ大手企業にとって、全社的な品質管理レベルの向上に直結します。
3.3 クレーム・リコールリスクの低減とブランドイメージの向上
不良品が市場に流出することは、消費者からのクレームや、最悪の場合、大規模なリコールに発展する可能性があります。これは、企業の社会的信頼を大きく損ね、回復には多大な時間とコストを要します。印刷検査装置は、こうしたリスクを未然に防ぐことで、企業のブランドイメージを保護し、長期的な企業価値向上に寄与します。
3.4 生産ライン全体の品質管理体制強化
検査装置から得られる詳細なデータは、品質管理部門にとって貴重な情報源となります。どの工程で、どのような欠陥が、どの程度の頻度で発生しているのかを正確に把握することで、根本的な原因究明と改善策の立案が可能になります。これにより、個別の問題解決だけでなく、生産ライン全体の品質管理体制を根本から強化することができます。
4. 【コスト削減】ミルクカートン印刷検査装置導入の経済的メリット
4.1 目視検査にかかる人件費の削減と人員配置の最適化
印刷検査装置の導入により、これまで目視検査に割り当てていた人員を大幅に削減できます。これにより、人件費という大きな固定費を削減できるだけでなく、削減した人員を他の生産工程や付加価値の高い業務に再配置することが可能になります。結果として、生産性向上とコスト効率の改善を同時に実現できます。
4.2 不良品発生による廃棄ロスの削減
印刷不良品は、そのまま廃棄されることになり、原材料費や製造工程にかかったコストが無駄になります。検査装置による早期かつ正確な不良品検出は、これらの廃棄ロスを最小限に抑えます。特に大量生産を行う大手企業においては、この削減効果は非常に大きくなるでしょう。
4.3 再印刷・再加工にかかるコストの削減
市場に不良品が流出してしまった場合、再印刷や再加工、さらには製品の回収といった追加コストが発生します。これらのコストは、単に製造費用だけでなく、物流費や人件費、そして機会損失にも繋がります。検査装置の導入は、こうした二次的なコストの発生を未然に防ぐための最も効果的な投資と言えます。
4.4 生産効率の向上とスループットの最大化
自動検査システムは、目視検査に比べてはるかに高速で安定した検査が可能です。これにより、検査工程がボトルネックになることなく、生産ライン全体の速度を維持または向上させることができます。結果として、生産スループットの最大化に繋がり、生産量増加による収益向上に貢献します。また、不良品排出が自動化されることで、手作業による仕分けや再確認の手間も省け、作業効率も向上します。
5. 導入検討時に押さえるべきポイントと選定のコツ
ミルクカートン印刷検査装置の導入は、貴社の生産体制に大きな変革をもたらす重要な投資です。失敗しないためにも、以下のポイントをしっかりと押さえて選定を進めましょう。
5.1 自社の生産ラインと検査要件の明確化
まずは、貴社の現在の生産ラインの状況、生産量、検査対象となる印刷物の種類(サイズ、素材、印刷色数など)を具体的に洗い出しましょう。そして、どのような種類の欠陥(色ムラ、ピンホール、印字不良など)を、どの程度の精度で検出したいのか、具体的な検査要件を明確にすることが重要です。これにより、過剰な機能を持つ高価な装置を導入したり、必要な機能が不足している装置を選んでしまったりするリスクを回避できます。
5.2 検査対象となる欠陥の種類と検出能力の確認
メーカーによって、得意とする検査対象や検出能力は異なります。事前に定義した検査要件に基づき、候補となる装置が目的とする欠陥を確実に検出できるか、デモンストレーションやサンプルテストを通じて検証しましょう。特に、貴社が最も懸念している種類の欠陥(例えば、特定の色の色ムラや極小のピンホールなど)に対して、十分な検出能力があるかを確認することが肝心です。
5.3 検査速度と生産能力の適合性
検査装置の導入目的の一つは、生産効率の向上です。そのため、導入する装置の検査速度が、貴社の生産ラインの速度や生産量と適合しているかを確認することは非常に重要です。いくら高精度でも、ラインの速度についていけない装置では、かえって生産性を低下させてしまう可能性があります。将来的な生産量増加にも対応できる拡張性も考慮に入れると良いでしょう。
5.4 導入後のサポート体制とメンテナンス
高機能な検査装置は、導入後のサポート体制が非常に重要です。装置の操作トレーニング、定期メンテナンス、トラブル発生時の迅速な対応など、メーカーのアフターサービスの内容を事前に確認しましょう。長期的な運用を見据え、信頼できるパートナーを選ぶことが成功の鍵となります。
5.5 費用対効果の評価と投資回収期間のシミュレーション
検査装置の導入には初期投資が伴います。しかし、人件費削減、廃棄ロス削減、クレーム・リコールリスク低減といった具体的な経済的メリットを数値化し、投資回収期間をシミュレーションすることで、導入の妥当性を評価できます。単なるコストではなく、将来の企業価値向上への「投資」として捉え、総合的な視点から判断することが重要です。
6. まとめ
本記事では、ミルクカートン印刷検査装置が製造業にもたらす品質向上とコスト削減という二大メリットに焦点を当て、その全貌を解説しました。
目視検査の限界を乗り越え、高精度かつ効率的な自動検査を実現することは、不良品流出リスクの低減、人件費や廃棄ロスの削減、そして生産性向上に直結します。これは、単なる設備投資ではなく、企業のブランドイメージ向上と持続的な成長を支える戦略的な投資と言えるでしょう。
貴社の生産ラインに最適なミルクカートン印刷検査装置を導入することで、品質とコストを両立させ、激化する市場競争において確固たる競争優位性を確立できるはずです。ぜひ、この機会に自動検査システムの導入をご検討いただき、次世代の品質管理体制へと進化させていきましょう。